Springboards
Springboards
Springboards are nothing more than a plank of wood with a steel shoe one end. But they revolutionized timber felling in the west.
As the loggers harvested timber in the northeast and the upper Midwest in the late 1800’s and early 1900’s, they were able to utilize all of the tree and were able to cross-cut the tree down from the ground. This maximized the utilization of the tree and left a lower stump for the horses to skid the logs over.
As the loggers moved west, they encountered trees 2, 3, and 4 times larger in diameter than in the east. Many of these trees were 200-500 years old. They encountered species they had not seen, Western Larch, Western White Pine, Western Red Cedar, Douglas fir. Many of these species, especially Western Larch had large “Butt Swells” where the sap and resins of the tree over its lifetime migrated and created these swells. On top of that, these swells had rot, fire scars, ring shake (Splitting on the fibers along the growth rings) and heart checks (long cracks in the wood, sometimes just one, many times radiating out like a spangle). These defects made the first 4-12’ of the tree worthless for the sawmill. Plus, all the resins “Gummed Up” the cross-cut saws making it almost impossible to pull the saw through the tree.
Someone, who’s name is lost in history thought if we could climb above this swell and stand on a platform, we could make one cut above the butt swell and leave all that worthless wood on the stump. As spring boards developed, they were usually 6-8” wide, about 5-6’ long and a couple inches thick. They were usually made of a light, but strong wood so they could pack them from tree to tree. A metal “Shoe” was developed (Usually by the logging camps blacksmith) that attached to the end of the board that had a curled-up lip that would seat into the notch the logger had chopped out. These lips had a slight radius that allowed the sawyer to move the board forward and backwards in the notch. Sawyers usually worked as a pair, and they each chopped a notch about waist high. (On opposite sides of the tree). These notches were only 3-4” deep, and usually 8-14” wide. It really didn’t take much of a notch to hold a 200-pound sawyer on his springboard. The curled-up lip was pushed up into the notch as the sawyer stood on the springboard. The radius of the shoes tip allowed for the sawyer to “walk” (Or rotate) the springboard forward and backwards pivoting on the shoes tip. This allowed the sawyer to walk the springboard forward to cut the undercut, then walk it backwards and be able to reach the back of the tree for the back cut.
Depending on the amount of butt swell there was, they would go up one-board high, or two or three or more to get above the swell. If they went two or more boards high, each sawyer needed another set of springboards. Each time they went up another board, they cut another notch in the tree about waist high and just offset from his last one. The sawyers had to figure out the lead or direction they would fell the tree and work their board notches backwards, so when they were on their second or third board high, they were facing the correct direction of the way they were going to fall the tree.
Felling the tree with springboards
Once the sawyers had their springboards in place, they took their cross-cut saw and sawed in about a third of the way through the tree. They put the saw aside and started chopping out their undercut. They started from the top and worked their way down until they met their saw cut. With the bottom already cut from the saw, the chips would split off fairly easily. They usually had specialized “Double-bit Falling axes” that had longer than normal handles to be able to reach to the center of the tree. The sawyers would take turns chopping away to create the undercut. They usually used their axe to gun-sight the under cut to properly align the direction of fall. To do this, they would put the axe head in the undercut and look down its handle to gun sight where they wanted the tree to fell. If it was off a bit, they would saw out a little bit, re-chop the undercut until it aimed in the direction they wanted. Many people don’t realize that a good sawyer (Back then and today) can actually control the direction of fall within a few feet. This is done by looking at the trees lead or lean and placing the under cut in the exact direction of fall.
Once the undercut was in place, the sawyers “walked” their springboard to the back of the tree. They put one boot under the board and one on top, and walked/bounced the board backwards and it pivoted on the shoes tip. This allowed them to cut both sides of the tree from a single notch saving time. They then started sawing the “Back cut” about 3-4” above the undercut. As they sawed, they placed wedges in the saw cut (Kerf) so the saw didn’t get pinched. As they sawed, they would oil the saw with kerosene, or in the case of Western Larch, a soapy water since Larch pitch is water soluble. These were either beer or whisky bottles with a curved metal hook attached so they could hook it in the bark of the tree to keep it handy. As they sawed their back cut and got closer to the undercut, the sawyers communicated how much “Holding Wood” was left. This holding wood allowed the tree to start falling in the exact direction of the undercut, holding the tree in that direction as it fell. Then as the undercut’s upper and lower cuts closed, it popped or broke the holding wood sending the tree to the ground exactly where they wanted it.
The old timers said the safest place for the sawyer as the tree fell was to stay on the spring boards.
Keeping history alive
Having a background in Timber Sports since college as well as being a forester for over 40 years, I had all the equipment and the access to trees to fall. I was able to pick out and save some standing larch in an up coming timber harvest and prior to harvest, keep the art of springboard falling alive.
The pictures are from several of our adventures. One thing I noticed is that when sawing with a crosscut, you don’t need ear plugs like with a chain saw. So, you can communicate with your sawing partner, hear the tree creek as it’s falling.
There are 100-year-old springboard stumps all over the northwest. As they decay, we’ve made a few in Idaho and Montana that will last another 100 years.
Today, Timber Sports still honor this technique of falling in the Spring Board Chop. The contestants use very similar springboards as they did 100 years ago, chop board holes in their “Tree’ and instead of sawing the tree, they chop the top off with razor sharp axes. They “perfect” board hold can be done in four hits and hold a 280 pound chopper.
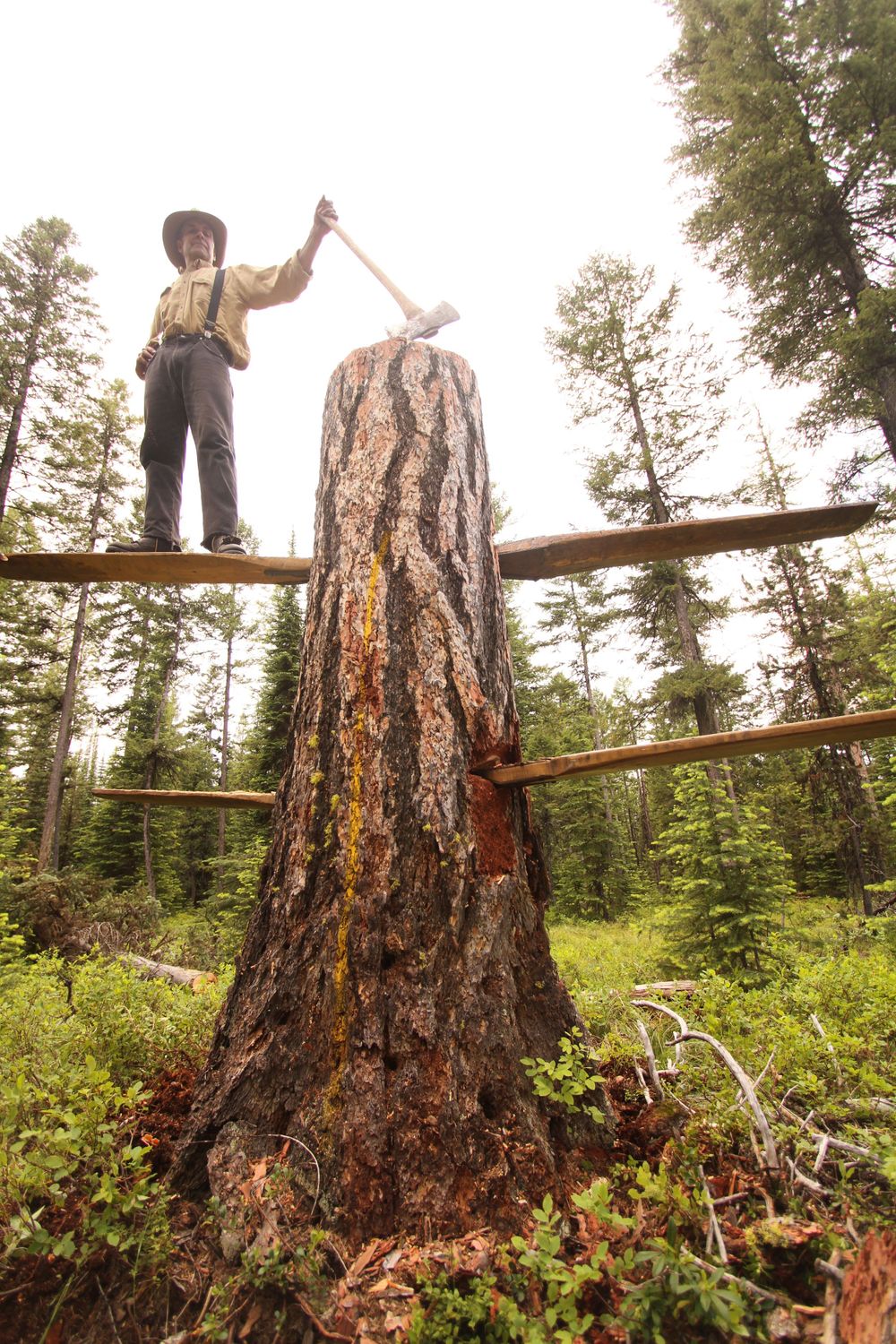
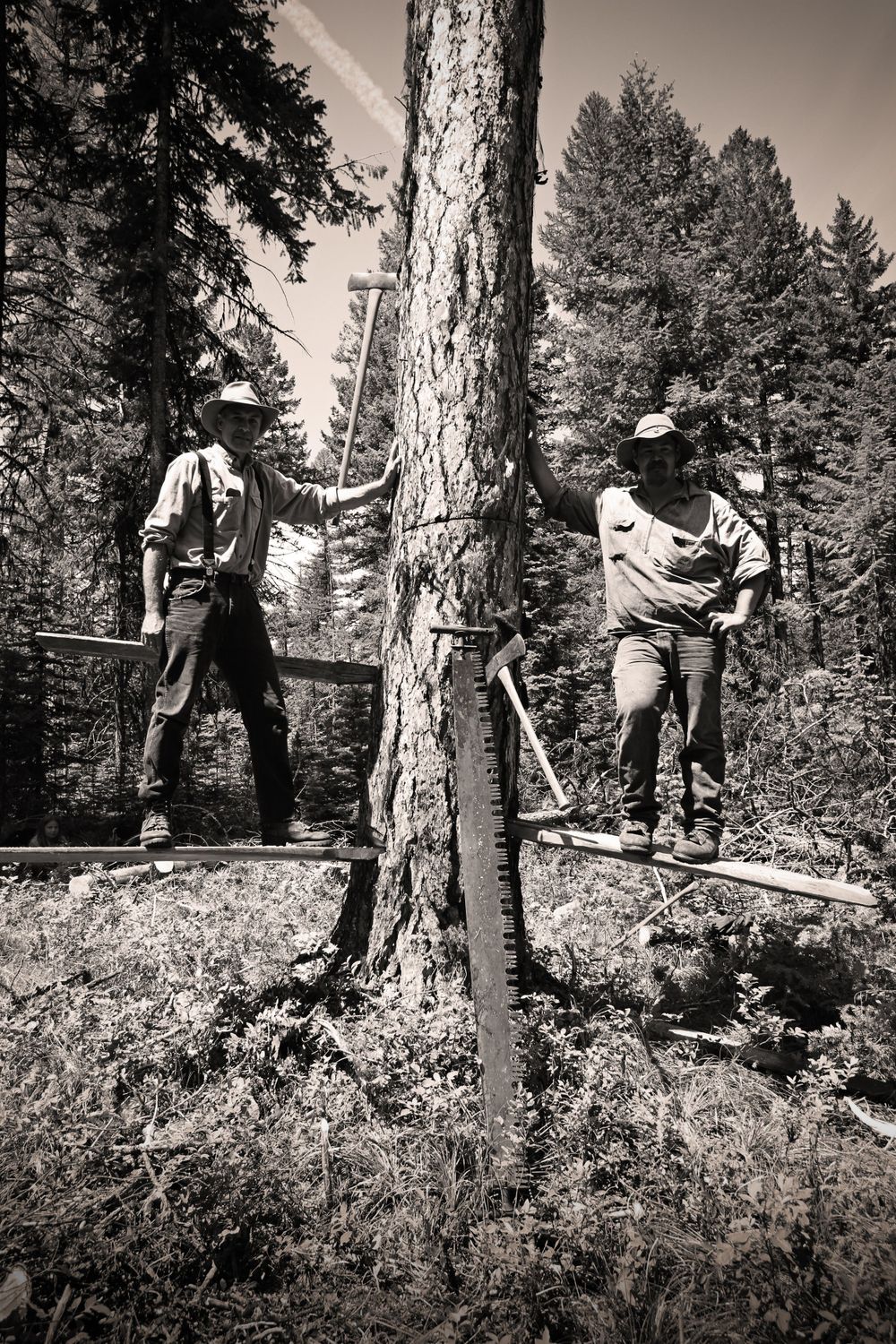
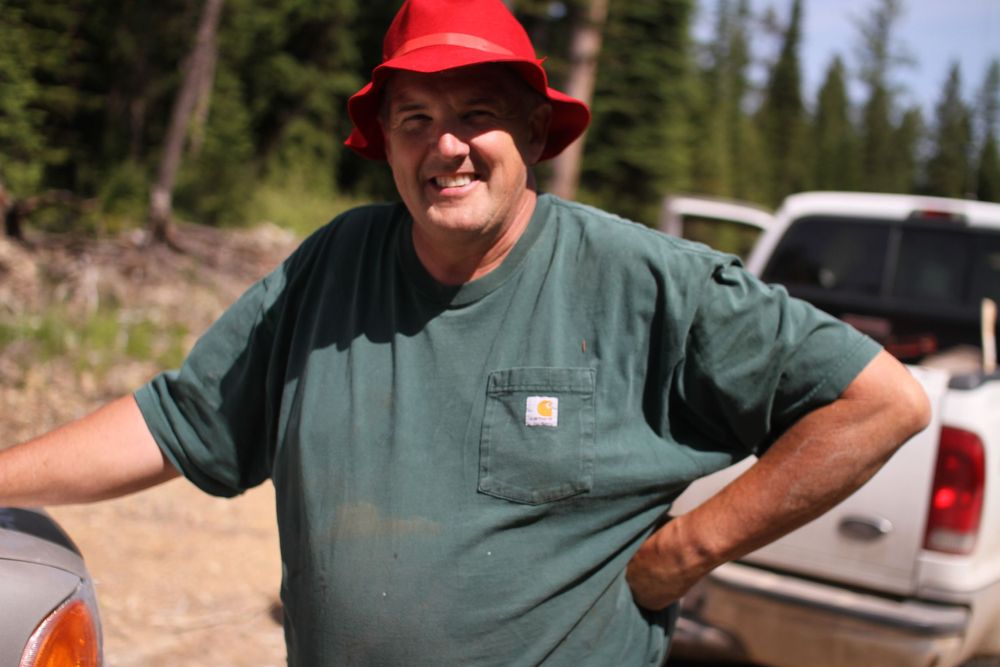
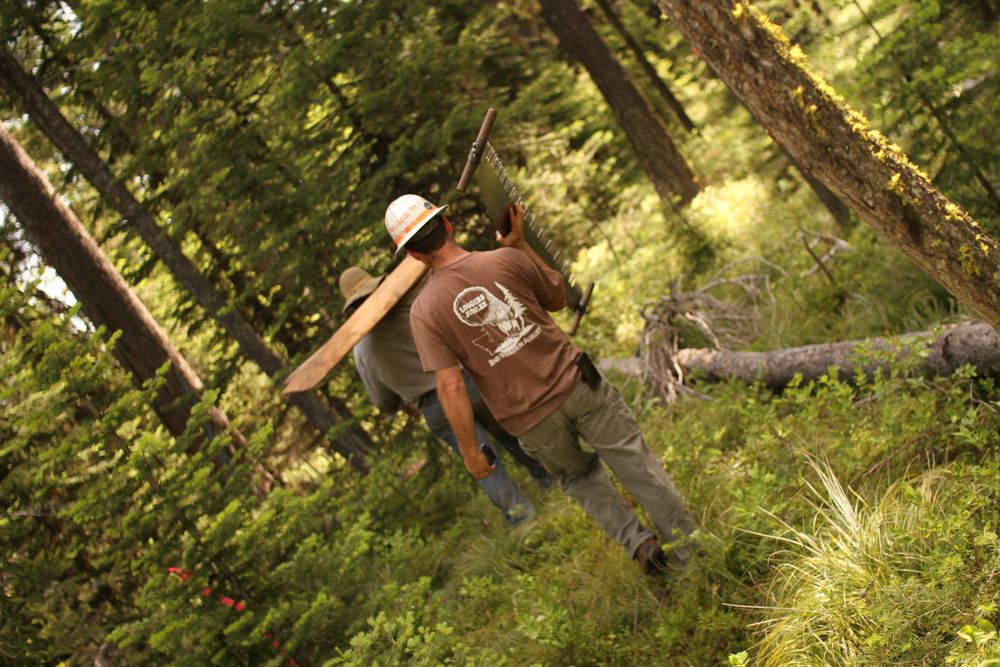
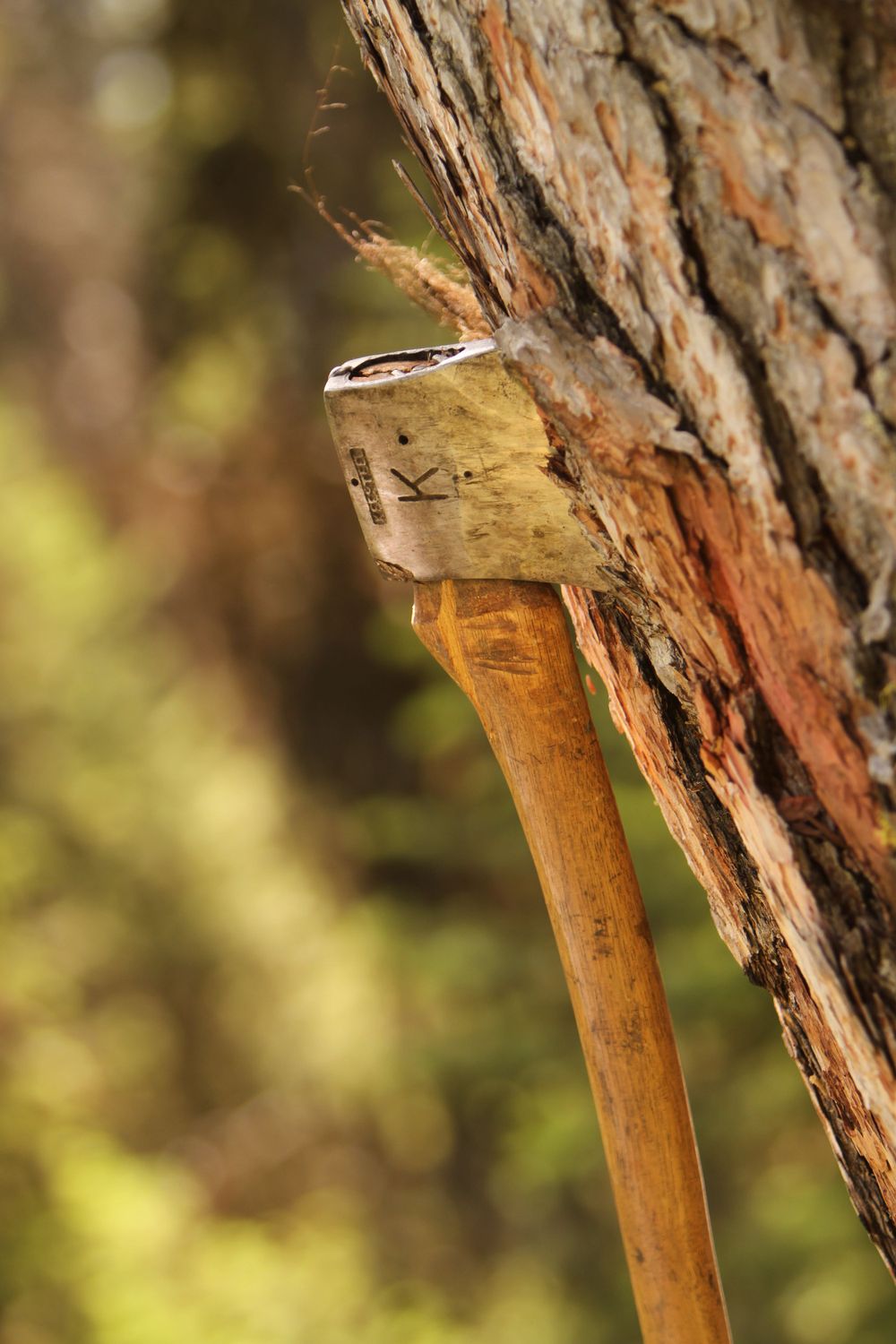
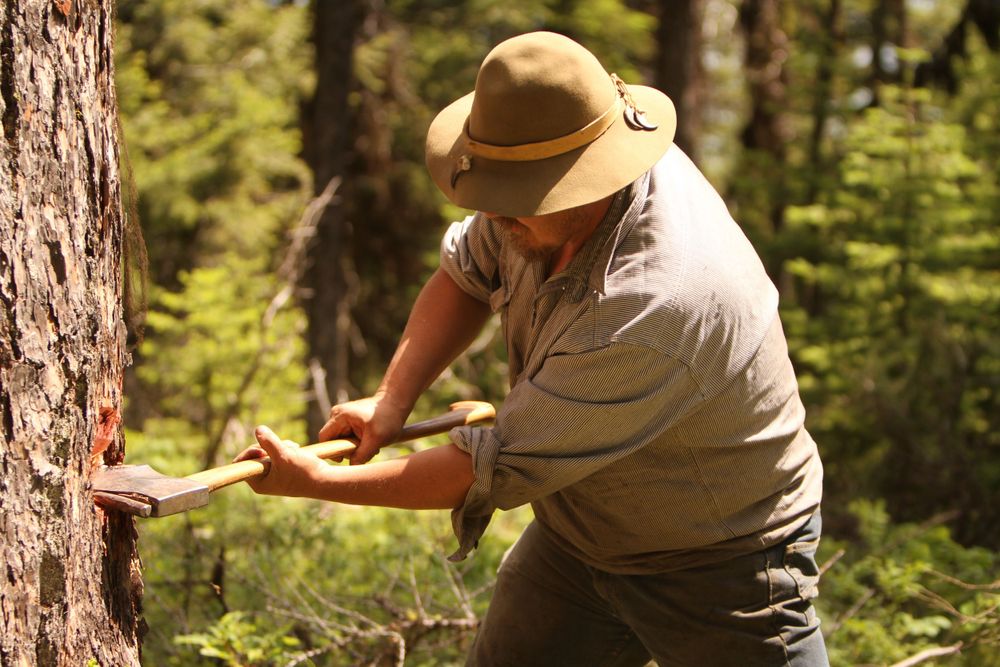
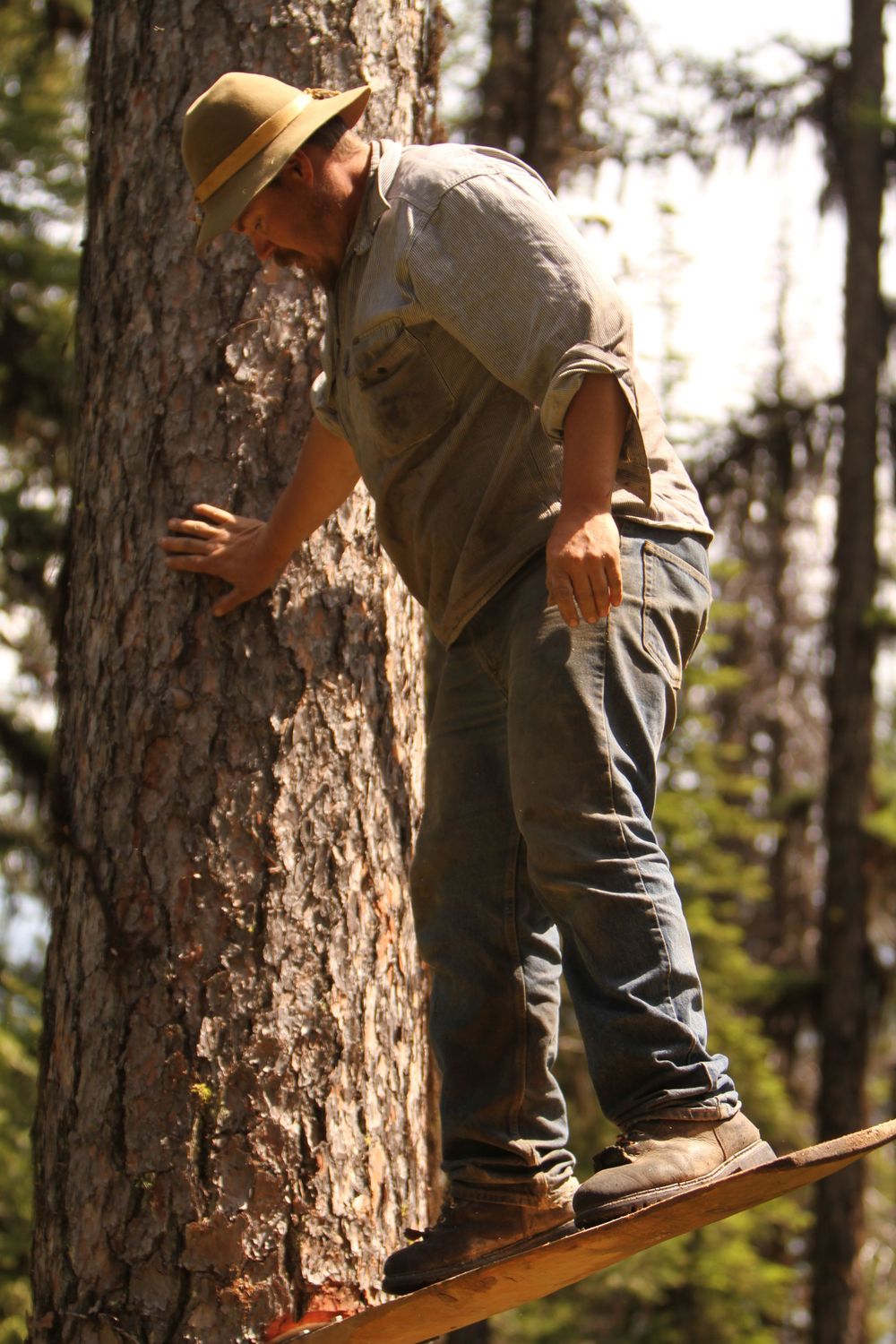
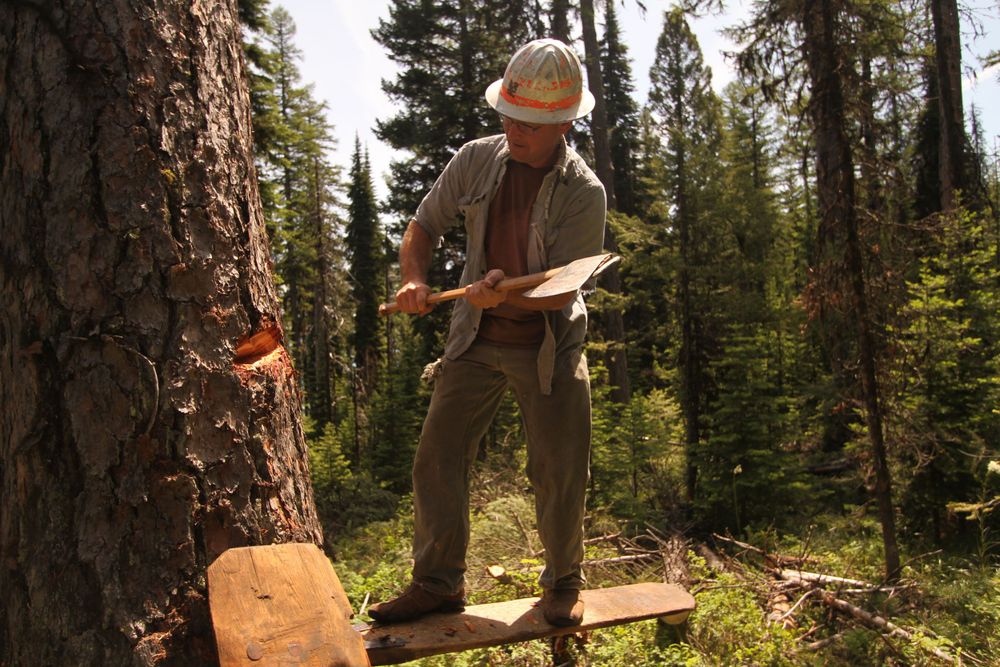
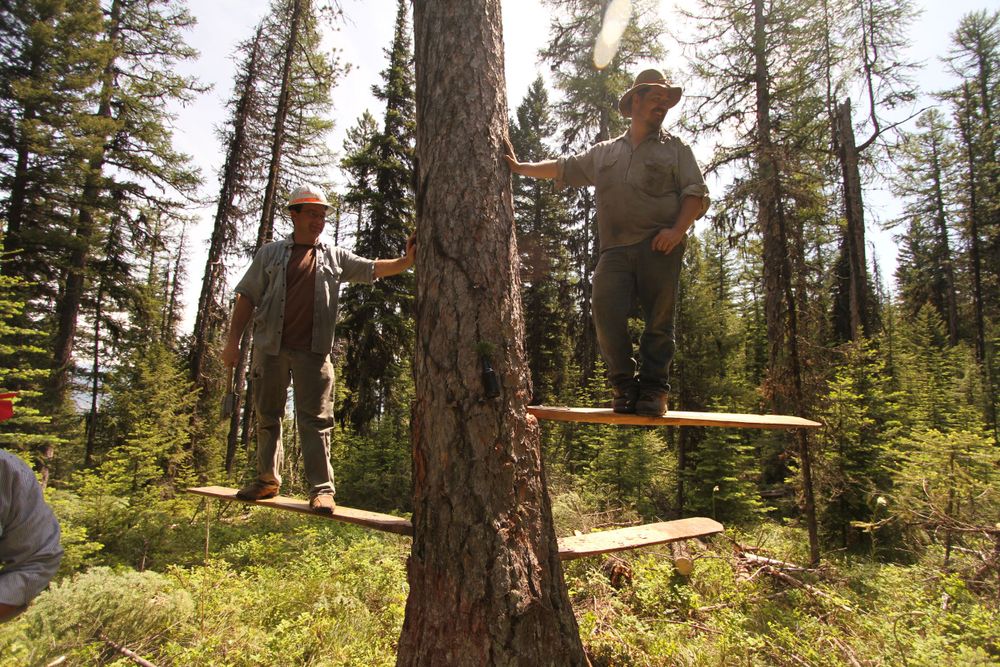
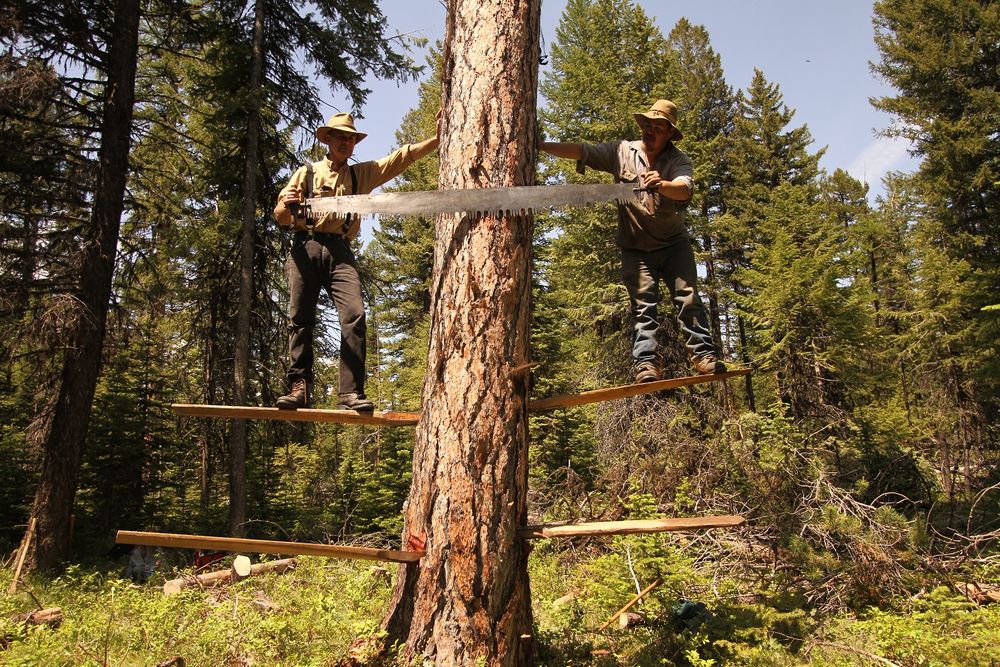
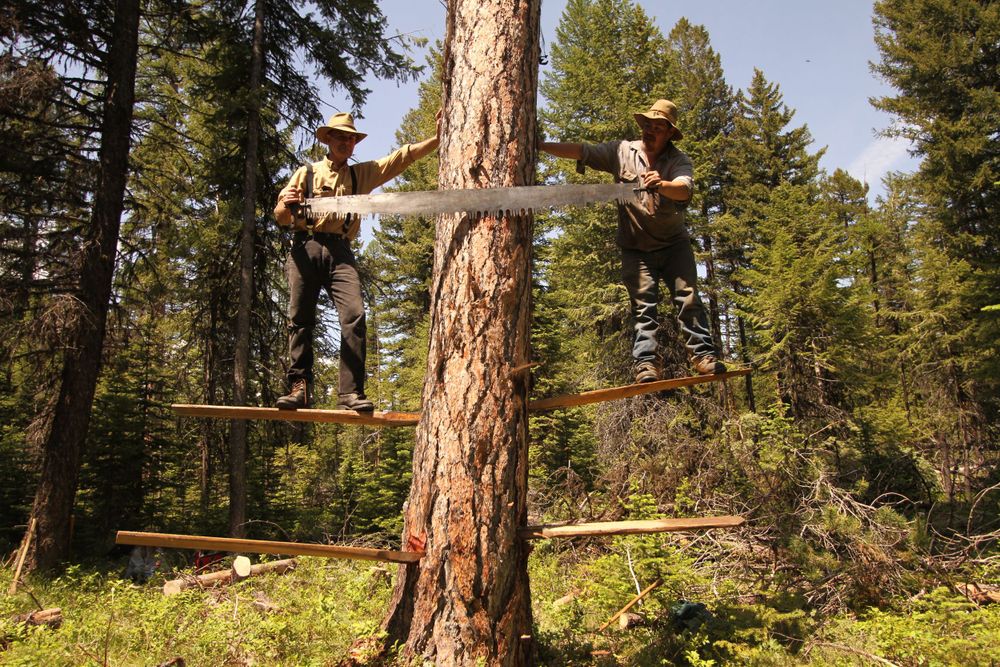
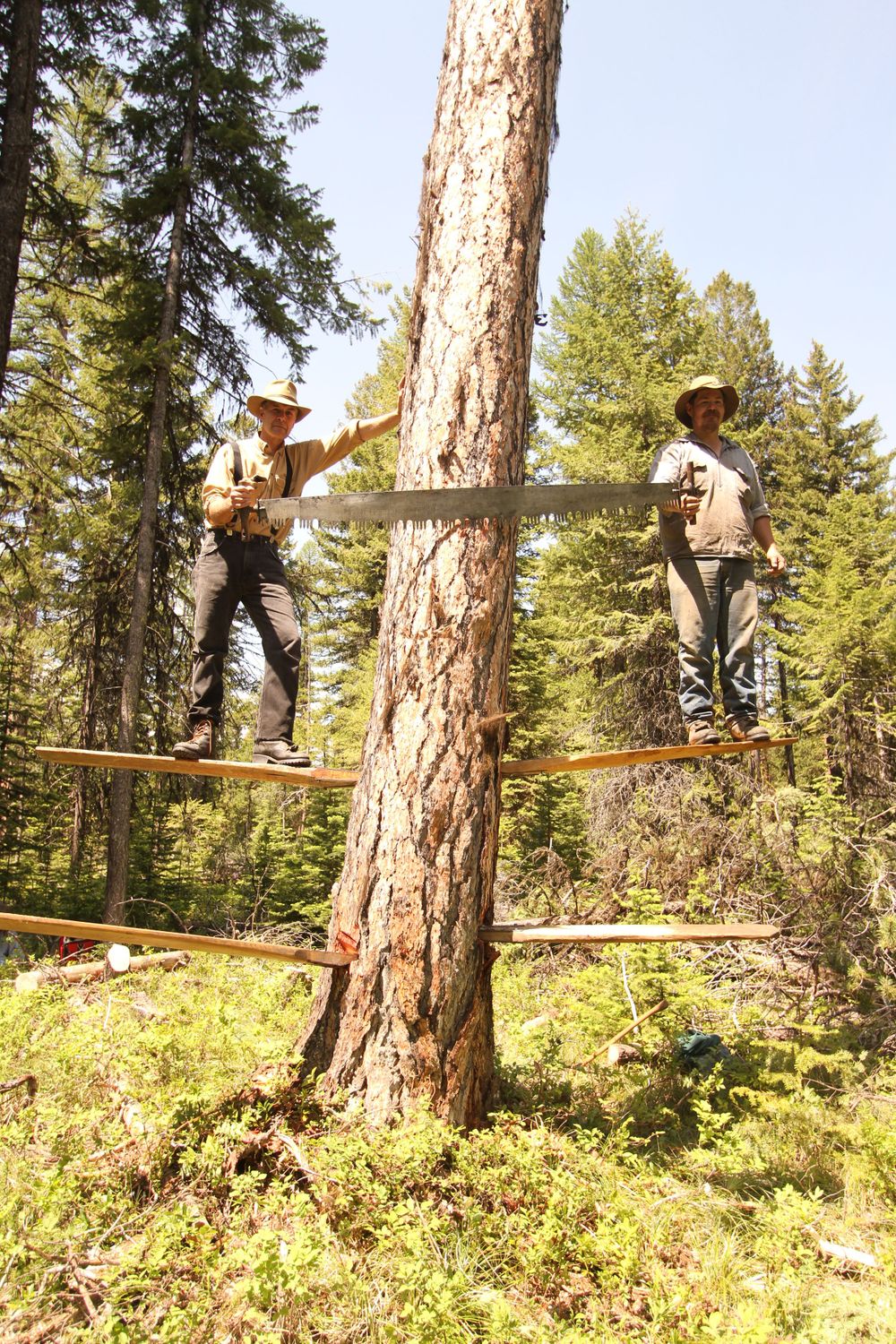
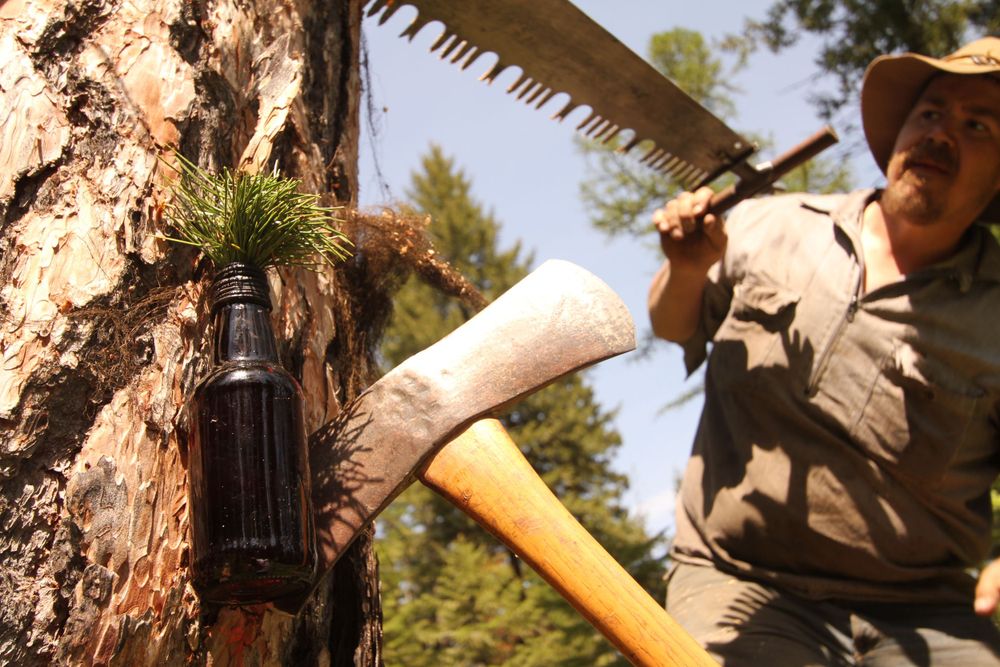
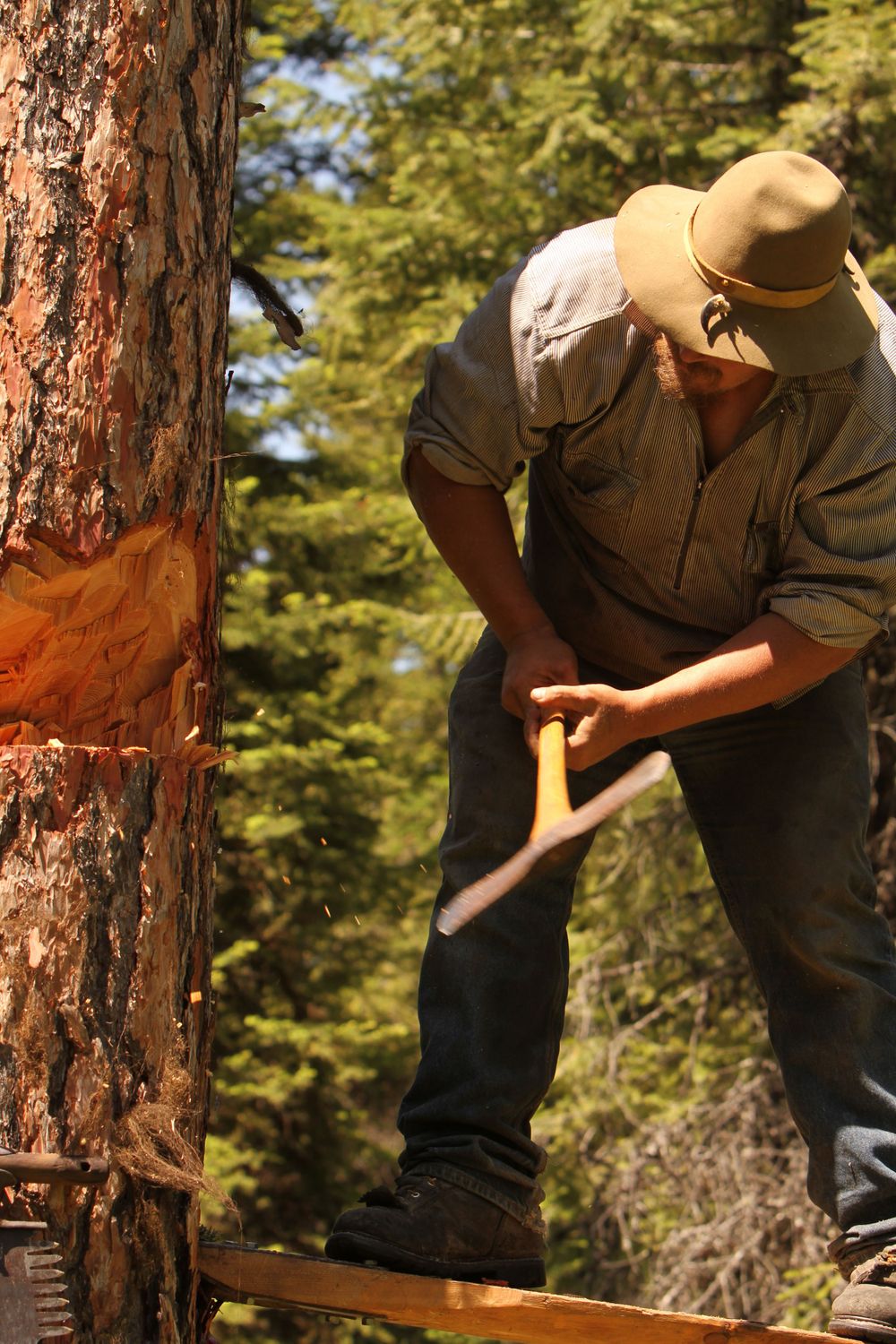
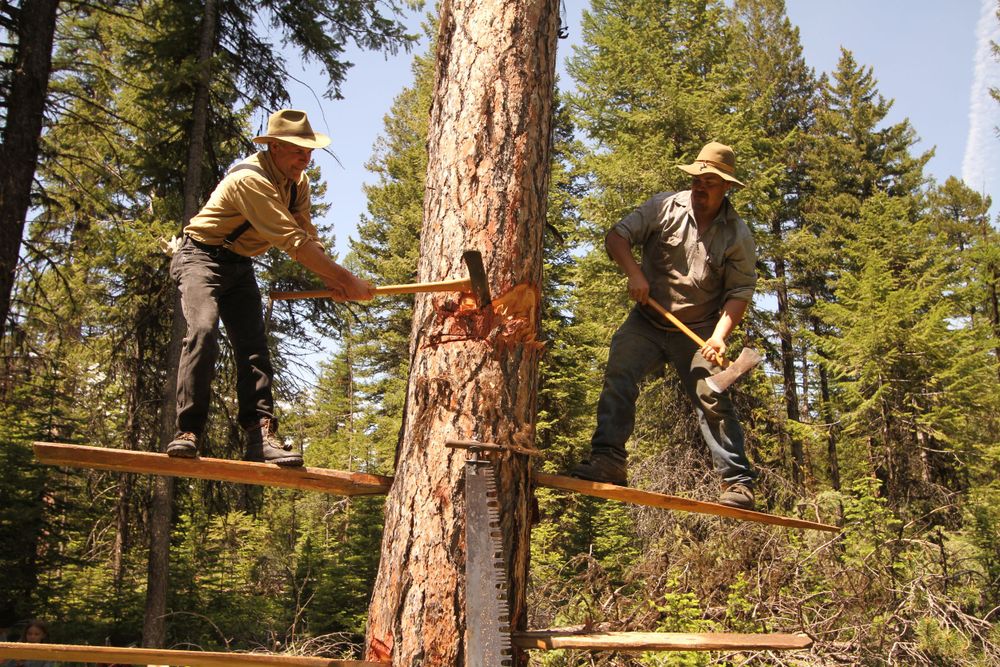